Features
What do we offer?
technologies for industrial Machine builders and End users.
Features
What do we offer?
technologies for industrial Machine builders and End users.
WELCOME TO NOUX NODE
Road to full utilization of the industrial ops
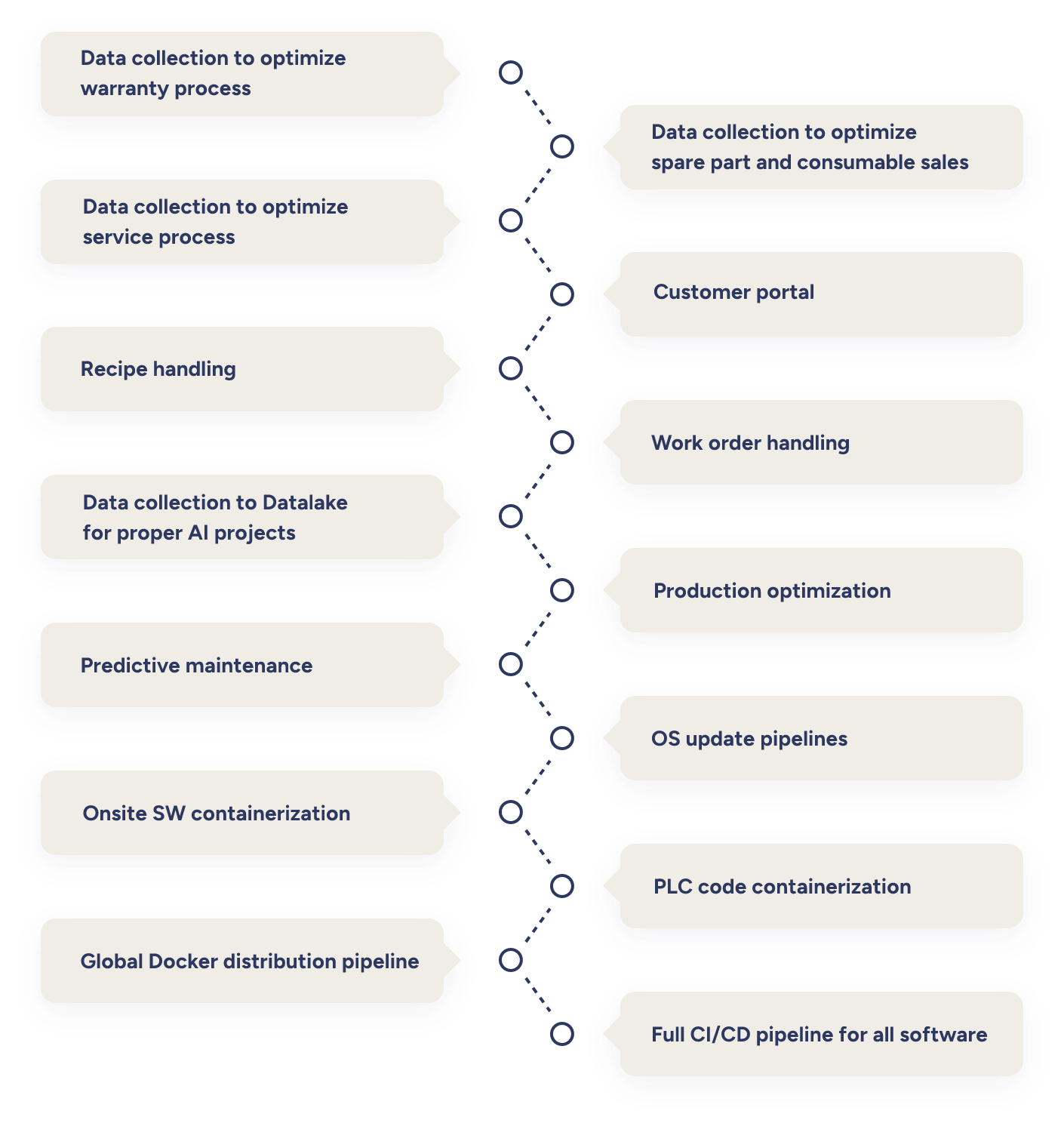
Data collection to optimize service process
By collecting data during the warranty period, the Original Equipment Manufacturer (OEM) can determine whether the user has misused the machine. This enables more effective troubleshooting without the need for special tools such as VPN or automation vendor tools.
Data collection to optimize spare part and consumable sales
For certain Original Equipment Manufacturers (OEMs), spare parts and consumables represent a substantial source of income and profit. Through the collection of machine usage data, one can accurately estimate the demand for these materials allowing the optimization of revenue and profit by offering the right products at the right time.
Data collection to optimize service process
Service engineers frequently possess an extensive toolkit for troubleshooting machines on-site, utilizing HMI panels and laptops to access error logs and service-related usage history. However, performing the same tasks remotely requires special tooling and is time-consuming. With dedicated data collection and pre-defined Service views, one can observe the current situation and review historical data efficiently. This minimizes the time spent on the case.
Customer portal
Many Original Equipment Manufacturers (OEMs) are frequently requested to provide various reports on the operations of their machines. Customers may also seek dedicated datasets or real-time information on their operations. By establishing a Customer portal with API interfaces to all datasets, OEMs can seamlessly fulfill these demands. This approach allows for the outsourcing of data ordering, as well as user and data access management, to its customers.
Recipe handling
Many industrial machines utilize recipes in their operations. The deployment of new recipes is typically synchronized with work orders from the central recipe bank to individual machines or among multiple machines. The distribution of recipes often involves a manual and intricate process. Centralized recipe handling system offers freely configurable recipe templates and effortlessly distribute them across individual machines and even multiple physical sites.
Work order handling
Industrial machinery users, such as factories, receive their work orders from the ERP system. Currently, the process of conveying this information to the machines is often manual, involving the distribution of printed papers to machine operators. By implementing a centralized work order handling process, all new orders, including required recipes, can be efficiently distributed to machines. This eliminates the need for local operator intervention.
Data collection to data lake
Machine learning and artificial intelligence are increasingly becoming integral to industrial processes. To harness the full potential of these technologies, data scientists require a substantial amount of high-quality data from industrial machinery. However, raw data from automation systems is often unsuitable in its original form for data scientists. The most effective approach involves cleaning, harmonizing, naming, and organizing the data at the source. Once prepared, it is securely transmitted to the data lake in the precise format and structure required by the scientists.
Production optimization
The optimization of an industrial process is frequently associated with Overall Equipment Efficiency (OEE) and its components: availability, performance, and quality. Enhancing efficiency can, in certain cases, result from straightforward monitoring and reporting feedback. Conversely, in more complex scenarios, sophisticated AI and ML models play a role in continuous process improvement. The selection of the appropriate approach is contingent upon the nature of the process, the operational maturity, available data, and expertise.
Predictive maintenance
Predictive maintenance is designed to anticipate service needs in advance, preventing unexpected downtime. Many Original Equipment Manufacturers (OEMs) possess in-depth knowledge of their machines, allowing them to formulate mathematical and logical rules based on collected machine and usage data. In some instances, these rules can be further enhanced through the use of appropriate machine learning (ML) and artificial intelligence (AI) models. However, this process is laborious and time-consuming, best implemented after human intelligence has been thoroughly leveraged
OS update pipelines
As one is delivering an increasing number of applications that necessitate the connection of machinery to the internet, operating system updates have become a crucial component of the requirements. This is particularly crucial for industrial Original Equipment Manufacturers (OEMs), given that the lifetime of these machines is often very long. An elegant solution involves the integration of professional Continuous Integration/Continuous Deployment (CI/CD) pipelines into all devices connected to the internet. This ensures the ability to control port settings, manage IP addresses, and execute operating system updates on these devices at any given day.
Onsite SW containerization
Many industrial machines incorporate non-real-time software components, such as visualizations or queue handling. The growing adoption of algorithms for predictions and optimizations is contributing to an increase in such software. The diverse range of these solutions poses a version handling challenge, as many are dependent on specific OS versions, libraries, and similar elements. To address this, modern solutions are turning to virtualization, opting for containerized solutions that make the usage of such software independent of the underlying device.
PLC code containerization
Traditionally, PLC software has been perceived as a device-specific solution due to the time-critical dependencies between the software and hardware. However, in a significant portion of installations governed by a PLC, the real-time requirements are low, and an acceptable level of jitter is present, making a virtualized software layer feasible. As the realm of IT solutions is progressively transitioning to virtualized approaches, it becomes evident that containerized PLC solutions will become increasingly prevalent. Given the benefits, such as hardware independence and simplified version management, the trend towards containerized PLC solutions is expected to accelerate.
Global container distribution pipeline
Virtualized software solutions offer undeniable benefits and are gaining widespread adoption in the industry. With a considerable amount of software delivered in containers, it becomes crucial to establish flexible distribution pipelines. Rather than depending on open marketplaces or vendor-specific app stores, it is essential to integrate private container registries into local virtualization layers. Integrating private container registries ensures a closed, cyber-secure system for managing the company’s global container fleet.
Full industrial DevOps solution
In the development phase of industrial solutions, DevOps practices align with the best standards in the IT industry. Nevertheless, achieving a similar level of sophistication on the operations side poses a considerable challenge, given that industrial components are not designed for continuous integration and deployment of new software versions. Moreover, obtaining continuous feedback from the processes is often a demanding task. Simultaneously, with increasing cybersecurity requirements and the need for flexibility in industrial processes, especially in the face of global competition, there is a growing need for a comprehensive DevOps process in the industrial environment.
WELCOME TO NOUX NODE
Road to full utilization of the industrial ops
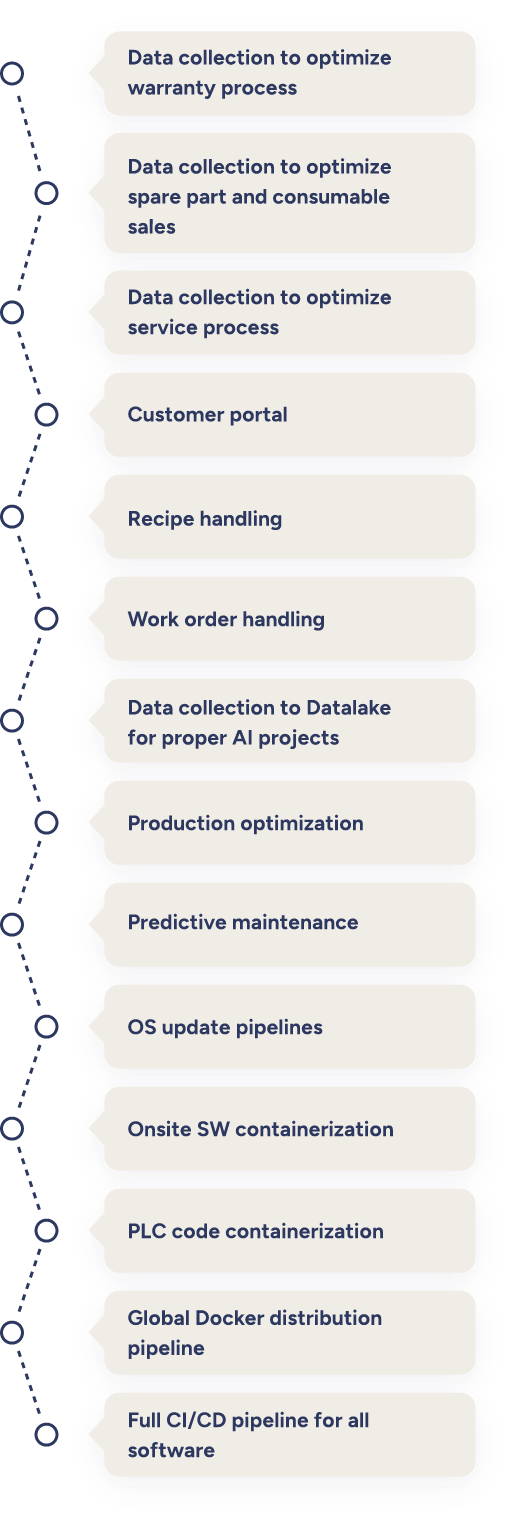
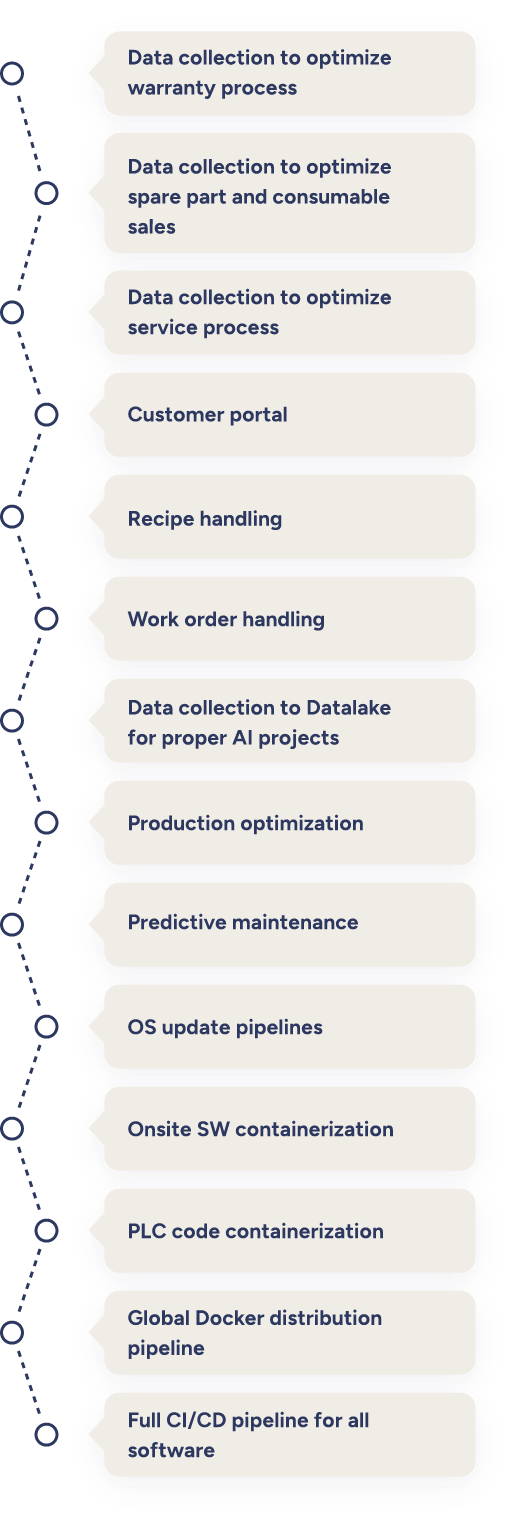
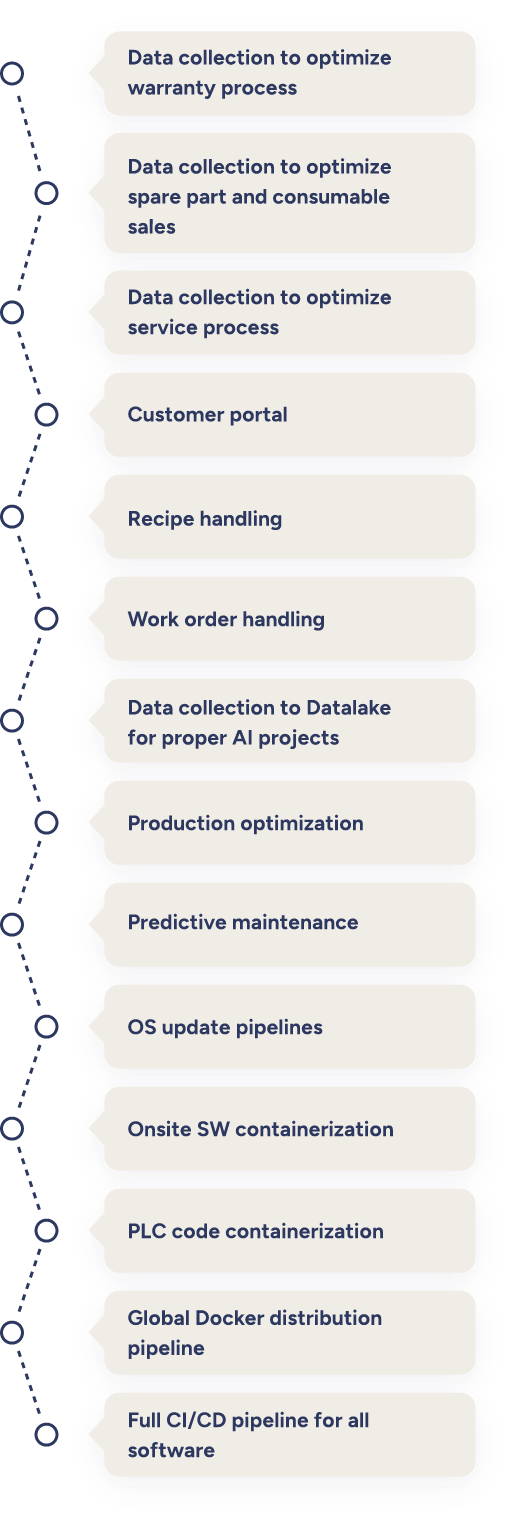
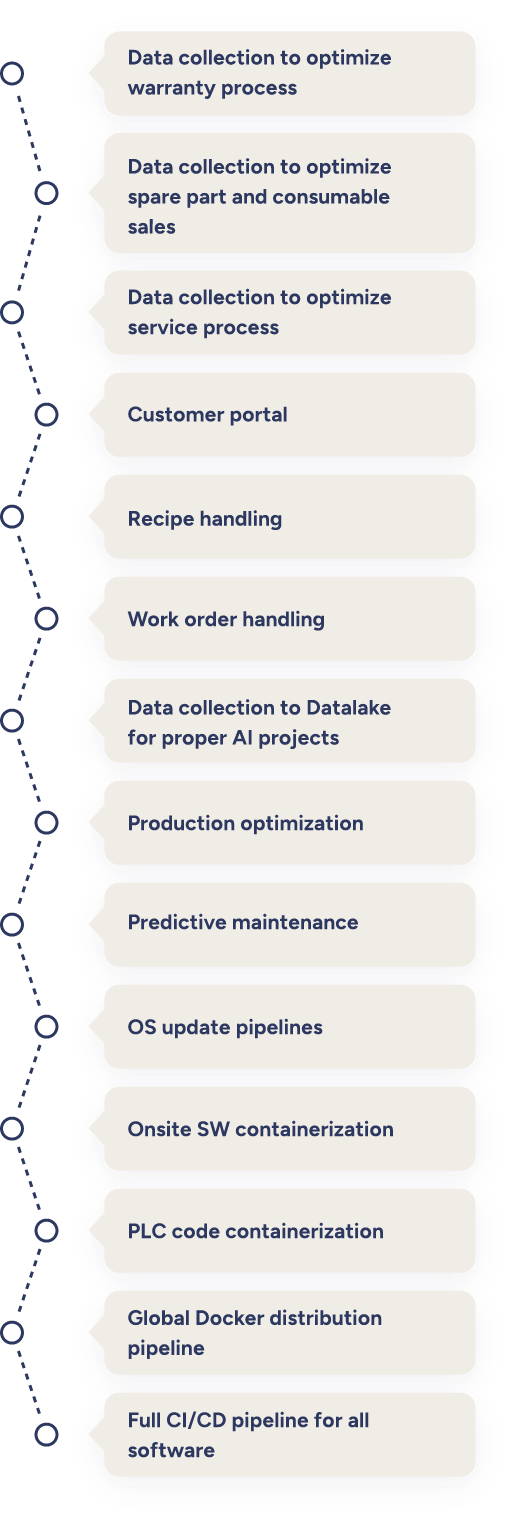
Data collection to optimize service process
By collecting data during the warranty period, the Original Equipment Manufacturer (OEM) can determine whether the user has misused the machine. This enables more effective troubleshooting without the need for special tools such as VPN or automation vendor tools.
Data collection to optimize spare part and consumable sales
For certain Original Equipment Manufacturers (OEMs), spare parts and consumables represent a substantial source of income and profit. Through the collection of machine usage data, one can accurately estimate the demand for these materials allowing the optimization of revenue and profit by offering the right products at the right time.
Data collection to optimize service process
Service engineers frequently possess an extensive toolkit for troubleshooting machines on-site, utilizing HMI panels and laptops to access error logs and service-related usage history. However, performing the same tasks remotely requires special tooling and is time-consuming. With dedicated data collection and pre-defined Service views, one can observe the current situation and review historical data efficiently. This minimizes the time spent on the case.
Customer portal
Many Original Equipment Manufacturers (OEMs) are frequently requested to provide various reports on the operations of their machines. Customers may also seek dedicated datasets or real-time information on their operations. By establishing a Customer portal with API interfaces to all datasets, OEMs can seamlessly fulfill these demands. This approach allows for the outsourcing of data ordering, as well as user and data access management, to its customers.
Recipe handling
Many industrial machines utilize recipes in their operations. The deployment of new recipes is typically synchronized with work orders from the central recipe bank to individual machines or among multiple machines. The distribution of recipes often involves a manual and intricate process. Centralized recipe handling system offers freely configurable recipe templates and effortlessly distribute them across individual machines and even multiple physical sites.
Work order handling
Industrial machinery users, such as factories, receive their work orders from the ERP system. Currently, the process of conveying this information to the machines is often manual, involving the distribution of printed papers to machine operators. By implementing a centralized work order handling process, all new orders, including required recipes, can be efficiently distributed to machines. This eliminates the need for local operator intervention.
Data collection to data lake
Machine learning and artificial intelligence are increasingly becoming integral to industrial processes. To harness the full potential of these technologies, data scientists require a substantial amount of high-quality data from industrial machinery. However, raw data from automation systems is often unsuitable in its original form for data scientists. The most effective approach involves cleaning, harmonizing, naming, and organizing the data at the source. Once prepared, it is securely transmitted to the data lake in the precise format and structure required by the scientists.
Production optimization
The optimization of an industrial process is frequently associated with Overall Equipment Efficiency (OEE) and its components: availability, performance, and quality. Enhancing efficiency can, in certain cases, result from straightforward monitoring and reporting feedback. Conversely, in more complex scenarios, sophisticated AI and ML models play a role in continuous process improvement. The selection of the appropriate approach is contingent upon the nature of the process, the operational maturity, available data, and expertise.
Predictive maintenance
Predictive maintenance is designed to anticipate service needs in advance, preventing unexpected downtime. Many Original Equipment Manufacturers (OEMs) possess in-depth knowledge of their machines, allowing them to formulate mathematical and logical rules based on collected machine and usage data. In some instances, these rules can be further enhanced through the use of appropriate machine learning (ML) and artificial intelligence (AI) models. However, this process is laborious and time-consuming, best implemented after human intelligence has been thoroughly leveraged
OS update pipelines
As one is delivering an increasing number of applications that necessitate the connection of machinery to the internet, operating system updates have become a crucial component of the requirements. This is particularly crucial for industrial Original Equipment Manufacturers (OEMs), given that the lifetime of these machines is often very long. An elegant solution involves the integration of professional Continuous Integration/Continuous Deployment (CI/CD) pipelines into all devices connected to the internet. This ensures the ability to control port settings, manage IP addresses, and execute operating system updates on these devices at any given day.
Onsite SW containerization
Many industrial machines incorporate non-real-time software components, such as visualizations or queue handling. The growing adoption of algorithms for predictions and optimizations is contributing to an increase in such software. The diverse range of these solutions poses a version handling challenge, as many are dependent on specific OS versions, libraries, and similar elements. To address this, modern solutions are turning to virtualization, opting for containerized solutions that make the usage of such software independent of the underlying device.
PLC code containerization
Traditionally, PLC software has been perceived as a device-specific solution due to the time-critical dependencies between the software and hardware. However, in a significant portion of installations governed by a PLC, the real-time requirements are low, and an acceptable level of jitter is present, making a virtualized software layer feasible. As the realm of IT solutions is progressively transitioning to virtualized approaches, it becomes evident that containerized PLC solutions will become increasingly prevalent. Given the benefits, such as hardware independence and simplified version management, the trend towards containerized PLC solutions is expected to accelerate.
Global container distribution pipeline
Virtualized software solutions offer undeniable benefits and are gaining widespread adoption in the industry. With a considerable amount of software delivered in containers, it becomes crucial to establish flexible distribution pipelines. Rather than depending on open marketplaces or vendor-specific app stores, it is essential to integrate private container registries into local virtualization layers. Integrating private container registries ensures a closed, cyber-secure system for managing the company’s global container fleet.
Full industrial DevOps solution
In the development phase of industrial solutions, DevOps practices align with the best standards in the IT industry. Nevertheless, achieving a similar level of sophistication on the operations side poses a considerable challenge, given that industrial components are not designed for continuous integration and deployment of new software versions. Moreover, obtaining continuous feedback from the processes is often a demanding task. Simultaneously, with increasing cybersecurity requirements and the need for flexibility in industrial processes, especially in the face of global competition, there is a growing need for a comprehensive DevOps process in the industrial environment.
Latest
news
Get up-to-date information and the latest headlines from us by subscribing to our newsletter.